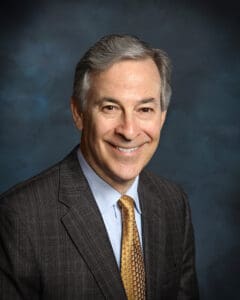
The upcoming Trump administration has signaled a number of trade and immigration initiatives that will significantly impact supply chain strategies for the next four years and beyond. The potential for business disruption and impact on the bottom line of many companies will cause the C-suites to turn to supply chain leaders to mitigate higher costs and labor shortages. This post focuses on what to do in what could be a very challenging labor market.
To understand what is happening and its impact on supply chain strategies, let’s look at what has been announced so far that could impact the labor market. It has been proposed that 2 to 11 million illegal aliens will be deported.
Before considering the impact of any efforts to remove illegal aliens let’s review what has been happening to the U.S. workforce for decades. The use of illegal aliens in the U.S. workforce has been well underway for over 50 years and, in many cases, embedded in the economic models of many industries such as construction, agriculture, domestic and janitorial services, landscaping, and many forms of manufacturing.
There are fewer U.S.-born people entering the job market because the birth rate in the U.S. has been declining for decades, and the birth replacement rate has not been met for 50 years. Further, the U.S. has been operating at almost record low levels of unemployment (3.7% to 4.1%) for 3 years and workforce participation has stabilized. This has consequences. From the middle of 2020 until today, supply chain organizations have been under intense pressure to find and retain quality resources – labor and knowledge workers.
Taking resources out of the U.S. labor market through mass deportation will put extreme cost and availability pressure on the overall labor market. As was seen during the pandemic, when there was also an extreme labor shortage, workers crossed industries to make more money. This is now a learned lesson for many workers and there is no reason expect that behavior to change as those industries most impacted by deportation or the threat of it, scramble to find workers to fill open positions.
The timing and level of deportation is uncertain, but when it does happen there will be resource scarcity shock waves rolling across industries and geographies. An obvious impact will be on the higher cost of those that are available. However, there is likely to be revenue impacts for those companies that cannot make up for the labor shortfall because they cannot get products to the market on time or at all.
The challenges retaining and recruiting supply chain talent have been underway for a number of years will increase. To mitigate the impact of impending tighter labor constraints, supply chain leaders will need to focus more of their efforts on becoming the employer of choice to retain and recruit resources while reducing their dependence upon labor in general.
The first action supply chain leaders should be on policies and practices that strengthen workforce retention. Replacement is going to get much harder because of an increasingly reduced pool of available resources and what we continue to hear from supply chain leaders, lower quality resources in the market.
The second action is to reduce the dependence upon supply chain labor and seasonal hiring. Supply chains are labor intensive, and the need for labor is not going away, but the impact of shortages can be mitigated through hard and soft automation. Repetitive tasks can be moved from humans to machines and robots.
The productivity of existing labor resources can be dramatically improved, reducing the number of manufacturing and warehouse workers and drivers needed or minimizing the need to hire as many seasonal workers as in the past. However, supply chain leaders need to act quickly here as we hear that lead times for automation equipment and resources to implement them has become extended.
The last action is to improve hiring practices and focus on non-cash benefits that attract new resources. Compensation will not be a differentiator unless your organization is willing to go well beyond industry norms for pay. At best, it will be temporal as others recognize your efforts. There are other ways such as flexible working hours, skills training, etc. that potential workers value highly and differentiate during the hiring process.
Two of the bigger wildcards in the deportation discussion are what industries and geographies get impacted first and the most. One way to look at this is to consider the states closest to the Southern U.S. border and their political leaning. For example, Texas and Arizona are more likely to see deportation move quickly than California. The same thoughts could be applied further inland. This is likely to affect smaller and regional rather than larger businesses as the larger ones have traditionally stricter hiring practices and greater regulations.
Supply chain leaders should also evaluate suppliers based on border or adjacent states to determine the vulnerability to a resource shortage. It’s not just whether they were using illegal aliens, but rather, are they at risk of losing labor to others willing to pay more to make up for their own shortfalls?
The U.S. labor market is extremely complicated and entwined and unwinding the illegal alien situation that has been evolving over the last 50 years. Because “illegals” are deeply embedded in many industries, there will be unintended consequences to the overall workforce and supply chains in particular.
Protecting the supply chain workforce will be critical for the next four years as they are becoming more valuable given an impending reduction in available workers and proposed tariffs dissenting offshoring. Supply chain leaders need to be able to communicate to the C-suite that there is significant potential for higher labor costs but, equally important, fewer workers, which could impact top-line performance.
Investment in solutions that improve worker productivity or eliminate traditional labor-based operations must be prioritized to minimize the upcoming impact on resources.
Chris Jones is a supply chain industry veteran with over 40 years of a broad range of hands-on leadership experience. He was Executive Vice President at Descartes Systems for 19 years leading Marketing, Services, Product Management and Development at various times during his tenure. He helps supply chain executives understand how to transform their operation’s performance and expand its impact on the business.
Foster Finley has over 37 years of industry and consulting experience. He was a Managing Director at AlixPartners, the global business advisory firm, and co-lead the firm’s global Operations Practice. He has a long track record of high-impact, complex project planning and execution for operations-intensive clients across many industries.