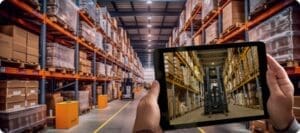
Flymingo is an Israeli computer vision company that identifies supply chain mistakes in operating processes in existing warehouse camera feeds. This is the only supply chain software company that the industry analyst firm ARC Advisory Group knows where AI Vision is core to the solution. They are using a form of AI for image recognition in conjunction with a warehouse management system. The solution is used to drive high adherence to standard operating procedures in a warehouse. SOPs are critical for safety and reliability.
Reinforcement Learning Applied to Computer Vision
Reinforcement learning is a form of machine learning that lets AI models refine their decision-making process based on positive, neutral, and negative feedback. For example, if you want to train a computer vision system to recognize a dog’s image, you will start by using humans to look at tens of thousands of images of animals. The humans label the pictures as dog, not dog, or unclear. The computer is then presented with those images. The system would say, “this is a dog” or this is “not a dog.” The dog recognition algorithm then receives feedback, either positive (yes, you are right, this is a dog), negative (no, this was not a dog), or neutral (we don’t really know if this is a dog or not). As the system goes through more and more feedback loops, its ability to correctly identify an image is honed.
In Flymingo’s solution, security cameras in the warehouse bring images of objects – pallets, trucks, cases, people, staging areas, and so forth – to the system. The system then identifies what type of object is being displayed. The combination of the image, data from the WMS, and contextual rules, then allows the system to understand whether processes are being followed.
How Do WMS and Computer Vision Work Together?
A warehouse management system is a category of application software that supports receiving, put-away, picking, shipping, and value added services. WMS solutions rely on automatic identification systems, often RF scanning devices that read barcodes, to record real-time status changes.
A WMS can drive almost perfect picking and inventory accuracy if SOPs are followed. A warehouse is set up with barcode labels on every slot in the distribution center. Barcode labels can also be placed on cases, pallets, and individual stock keeping units. For example, the WMS tells a floor associate to go to location AX32 and pick two cases. The associate goes to the location, scans the slot barcode label to confirm that he is in the right location, and scans the barcode labels on two cases, which proves that the right number of cases have been picked. Using a WMS in conjunction with AutoID can drive inventory accuracy of over 99.9%.
While a WMS can drive very high accuracy, much higher than any paper-based system, achieving those levels of accuracy depends upon workers not getting distracted and following the SOPs. For example, if a worker goes to the correct slot, and a coworker walks by and starts a quick conversation, the associate might inadvertently pick cases from the wrong slot when he turns back to the rack. Or an associate might be instructed to put a shipping label on a pallet when it is staged in a designated location near the dock. The associate may click a button on his RF device to start the label printer. She is supposed to go get the label, return to the pallet, and put the label on the pallet. However, if she decides to take a restroom break before going to the label machine, a different associate might take her label.
Flymingo’s computer vision system, in conjunction with the WMS, can identify that an error has likely occurred. In the example of putting a shipper label on a staged pallet, the vision system might be set up to flag a potential error if the associate does not return to the pallet location within three minutes. The associate’s manager can be alerted of a particular type of mistake, look at the footage, and determine whether a mistake has, in fact, been made. The manager can then rapidly engage in visual-based coaching. Near real-time feedback enhances workforce performance.
Not all errors result from mistakes. Some associates intentionally violate SOPs. For example, if a warehouse has performance targets, an associate may be told to go to a particular location and pick two cases. They might choose to make up time by not going to the location. Instead, they use their mobile device to indicate that there is no inventory in the slot. In short, they incorrectly assert that the pick could not be made. Or a thief on the shipping dock might intentionally put a pallet in an associate’s truck. In these cases, visual intelligence can be used to detect untrustworthy employees.
Cool Technology, But Does it Work?
Avi Boas, the chief of operations at Abaline, spoke at the Made4net user conference, Inspire 2024. Abaline is a private family-owned distributor with 25 trucks. Abaline’s primary distribution center is a 165,000-square-foot facility located in Bayonne, NJ. The distributor also serves healthcare facilities, educational institutions, and other sectors.
Abaline uses the Made4net WMS solution. Implementing Flymingo on top of the WMS allowed them to significantly improve process adherence. Mr. Boas said that before Flymingo was implemented, they might not have learned they had shipped the wrong medical supplies to an overseas customer for weeks. At that point, he and the shift manager might spend hours looking at stored security footage to determine what went wrong. When the manager talked to the associate about their mistake, the associate would frequently be defensive and blame the mistake on something beyond their control.
Now, the mistake is determined in near real-time. When the employee is approached, that associate can often figure out the mistake they made before the manager even broaches the subject. In addition to improved employee relations, better process adherence has improved customer service.