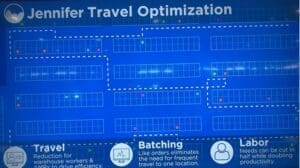
Warehouse management systems, once known as supply chain execution systems, have evolved significantly. They have transitioned from mere work executors to planning solutions with optimization capabilities. This transformation was brought about by the incorporation of algorithms that enhanced worker productivity. Today, for many professionals, “WMS” is synonymous with “warehouse optimization.”
It shouldn’t be. Optimization is no longer limited to WMS software. Adjoining systems—like Voice Recognition, Vision-directed Workflow solutions, and Robotics solutions—can also provide significant warehouse optimization capabilities.
Lucas Systems, a seasoned player in the industry, is a prime example. Founded 26 years ago, Lucas Systems has long provided voice recognition solutions. Their Jennifer solution has facilitated an astounding 100 billion picks!
Voice Recognition, a type of Automatic Identification, offers practical advantages. It can perform the same tasks as a traditional warehouse management system using barcode scanning. For instance, a Voice system can guide a worker, in their native language, to a specific location in the warehouse. The worker can confirm the location by speaking it, eliminating the need for an RF scan. Similarly, the system can instruct the worker to pick a certain number of items, and the worker can confirm the pick verbally, again avoiding the need for barcode scanning.
One of the significant advantages of a Voice solution is its focus on worker safety. By allowing users to keep their eyes on the task at hand, without the need to look down at a computer screen or reach for a holstered scanner, Voice Recognition technology reduces the risk of accidents while simultaneously increasing the speed of picking. Workers also improve their picking accuracy by keeping their eyes on a task. Accuracy is critical to warehouse operations. Many companies overlook the cost of order fulfillment mistakes, grossly underestimating their impact on the bottom line.
In a survey I did years ago, the main benefits of Voice were that it was easier to make new workers productive, there was an increased ability to use nonnative speakers, Voice was easier to use in freezers, and there were fewer injuries.
Until a recent briefing with Lucus, I tended to think of Lucas as a company that provided a Voice solution. Ken Ramoutar, a senior executive at Lucas, said that when the company started, there wasn’t good voice technology for industrial environments like warehousing. “So, Lucas had to build and invent much of that technology. But Voice has come a long way.” Voice, as a technology, has become commoditized.
Lucas began pivoting toward becoming an optimization company in 2017 when it introduced dynamic task prioritization and pick-path optimization.
With dynamic prioritization, planners assign priority codes and work groupings that allow related tasks to be grouped. Then, the work is dropped to the associates. But that work can be dynamically changed throughout the day.
Kyle Franklin, a senior solution consultant at Lucas, gave a simple example. Assume that a FedEx truck is scheduled to arrive at noon, a UPS truck at 3:00, and a United States Postal Service truck at 4:30. The orders associated with the FedEx truck, the first parcel truck to arrive, become Group 1. UPS orders become Group 2, and USPS becomes Group 3. “From 6:00 in the morning until, let’s say, 10:00 AM. I can be greedy.”
Work can be batched and optimized to minimize travel and thus maximize throughput. But then, at 10:00 AM, as the cutoff for FedEx picking approaches, the switch is flipped, and all the pickers focus on completing all the orders that must be picked for the FedEx truck. Once those orders are done, the system can again focus on full optimization until the following cutoff approaches. Directed workflows can become much more complex than this example suggests because Lucas can also support pallet picking, case picking, and rainbow pallets in addition to each picking.
Once the work has batched, the system works on path optimization. Lucas starts with a digital map of the warehouse. “We run traveling salesman algorithms to define the best pick path through the warehouse,” Mr. Franklin continued. “So, should I (a worker) take this cut through here? Should I double back here?”
But batching and path optimization work together for increased synergies. When a user says, “Get work,” they get the highest order in the prioritization queue. That becomes a “seed” around which other work is sequenced. The seed creates a travel-efficient path. Then, any additional eligible orders along the path are added to the worker’s task queue.
In 2022, they introduced slotting based on machine learning. In other words, the most picked items in the warehouse are given prime locations close to a loading dock. The Lucas solution allows slotting to occur on an ongoing basis rather than merely every few quarters. Then, last year, the company introduced its Next Generation Warehouse Optimization Suite based on a modern microservices architecture.
For companies with legacy WMS or old versions of WMS that have not been upgraded, implementing Lucas can be a much quicker, less disruptive, and less expensive way of achieving optimization. According to Lucas, Voice can improve productivity by 10-15%. That is credible, especially if workers have been picking based on paper instructions. Then, when companies add Lucas’s optimization, they can get an extra 10-40% boost in productivity. Again, this is credible for companies without any existing optimization solution. Finally, if a company is using dumb robotics, optimizing the robots can add another 5-20% in productivity. In short, there can be quite significant gains in throughput with Lucas. Payback, Mr. Ramoutar says, often occurs in less than 12 months.